On April 8th, 2024, the production base of Zhongpeng International Ceramics (Uzbekistan), constructed by HLT&DLT, successfully ignited the "4.0 Energy Efficiency Benchmark Smart Era" high-end glazed tile production line.
This milestone is expected to significantly enhance Zhongpeng International Ceramics (Uzbekistan)'s brand competitiveness in the Central Asian market.
It is reported that this production line is currently the largest in Uzbekistan in terms of output and the most representative modern production line with intelligent automation.
The successful ignition and production of this project undoubtedly establish a new benchmark for the local ceramic industry, bridging the gap in the high-end market of the Central Asian ceramic production areas. This initiative bolsters Zhongpeng International Ceramics (Uzbekistan)'s confidence in expanding and thriving in the Uzbekistan market.
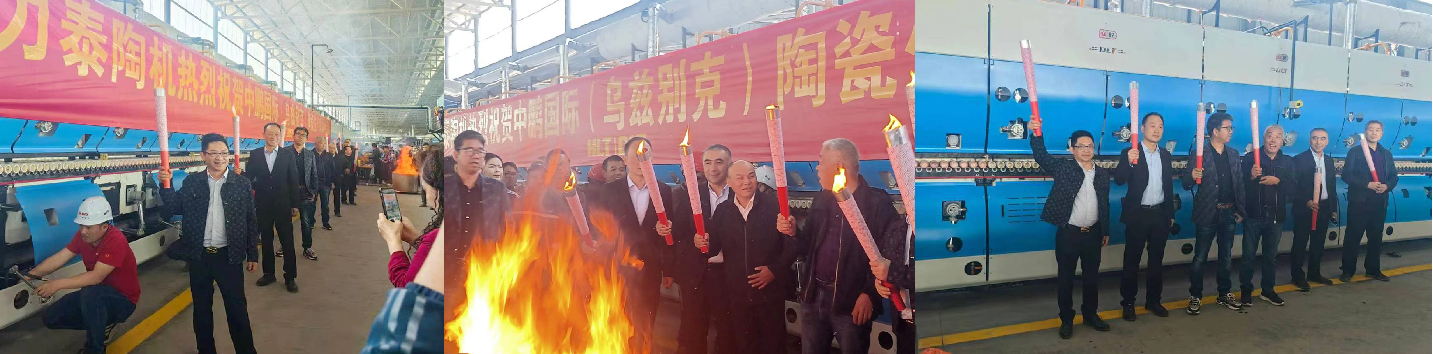
The first-phase project focuses on introducing 4 sets of classic and best-selling YP4009 presses from HLT, along with core thermal machinery from DLT, including an industrial "4.0 Energy Efficiency Benchmark Smart Era" high-end firing kiln, and a DHD-EM energy-saving self-circulating six-layer dryer.
The main production specifications include high-end rustic tiles and full polished glazed tiles with dimensions of 600*600mm, 800*800mm, 600*1200mm, 750*1500mm, and thickness ranging from 9-12mm. The production capacity is 50,000 square meters per day, and it is planned to reach 100,000 square meters per day after the completion of the second phase construction.
YP4009 Automatic Hydraulic Press
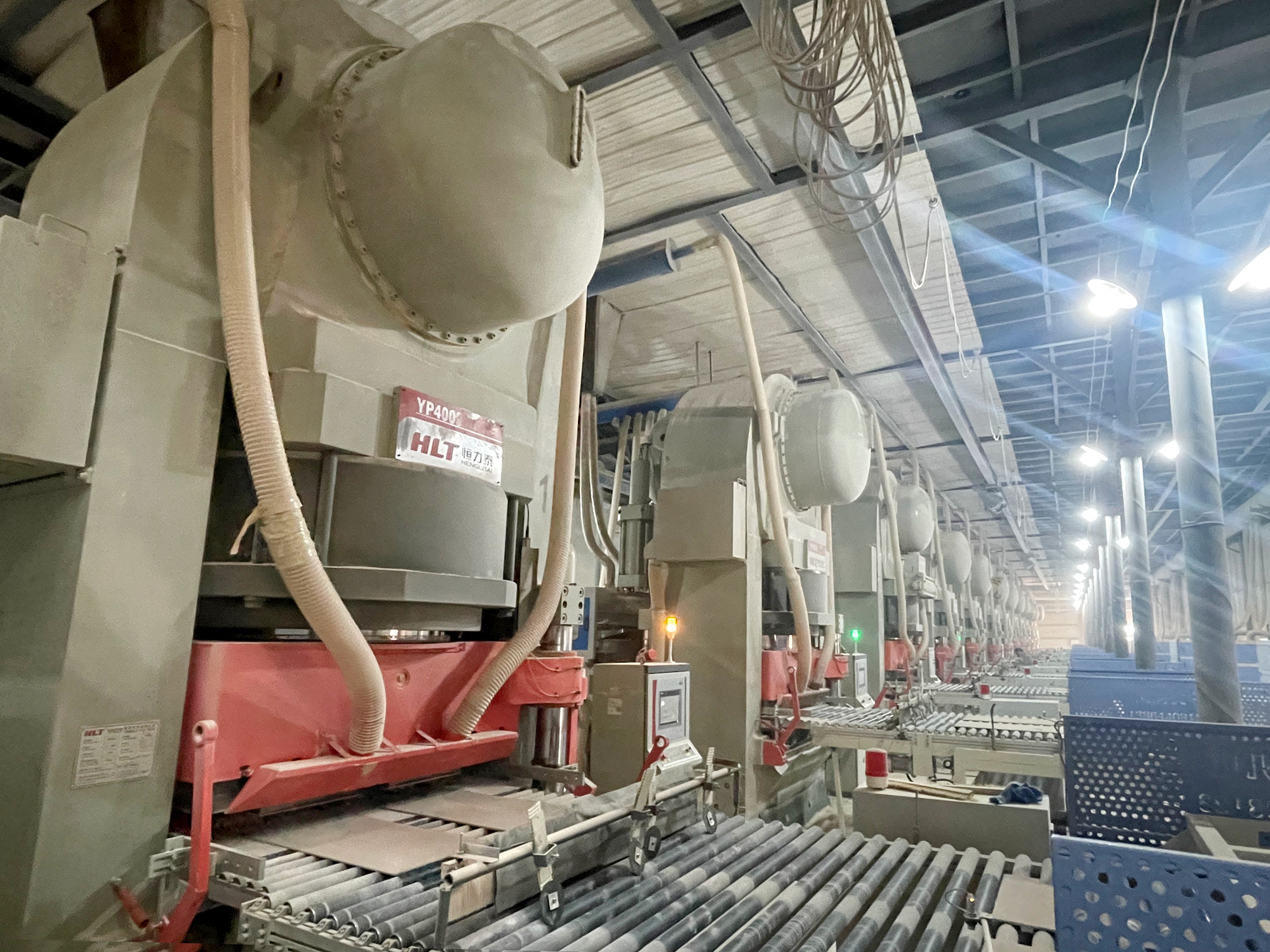
YP4009 represents an upgraded version of the energy-saving benchmark press from HLT and stands as one of the most classic models in the YP09 series. This press integrates multiple patented technologies, featuring a maximum pressing force of 40,000kN and an empty cycle frequency of up to 20 times per minute. As a result, it has garnered significant favor among customers in China and internationally. It features the following technological characteristics:
- The mainframe structure incorporates a new type of prestressed steel wire winding structure, providing exceptional fatigue resistance and load stability.
- Using the established external main cylinder structure from HLT, the main cylinder ensures stable and reliable operation with remarkably low failure rates, thus simplifying maintenance procedures.
- This press ensures good filling and drainage quality with rapid pressing speed, which adopts a new type of downward large-diameter springless filling valve.
- The booster is vertically installed and incorporates a displacement sensor for real-time monitoring of the booster piston's position, enabling flexible adjustments as needed.
- The hydraulic system can effectively enhance comprehensive performance metrics such as pressing speed and position accuracy. Due to the incorporation of various advanced technologies such as speed-boosting system, dynamic moving beam position closed-loop control, main cylinder pressure closed-loop control, and servo ejection device.
- Furthermore, the control program of the latest architecture program version ensures high repeatability of control actions and provides more flexible and convenient operation.
The "4.0 Energy Efficiency Benchmark Smart Era" High-end Firing Kiln Combination
The firing kiln is equipped with the DLT DDI4.0-A digital intelligent control system, enabling cloud computing and comprehensive management of the production line. This breakthrough in time and space allows for remote monitoring of the production line, providing comprehensive insights into machinery operation status.
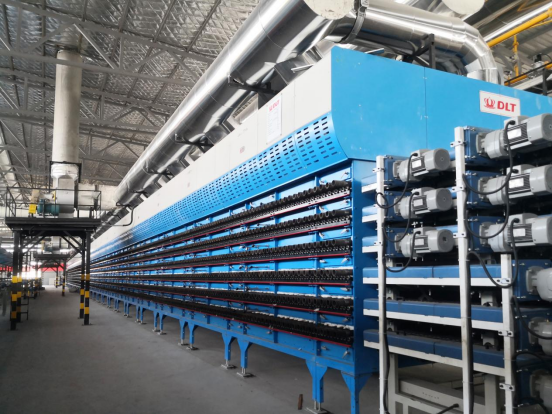
Designed to meet first-level energy efficiency standards, it incorporates high-configured systems such as the DLT patented technologies KPR assisted combustion heating energy-saving system, EHI kiln body insulation upgrade system, PPC assisted combustion air grouping control system, and DHR-plus efficient-relay waste heat recovery upgrade system.
The combination maximizes energy savings and automation effects due to coupled with the six-layer self-circulating dryer renowned for its high efficiency, uniformity, rapidity, and energy-saving features.
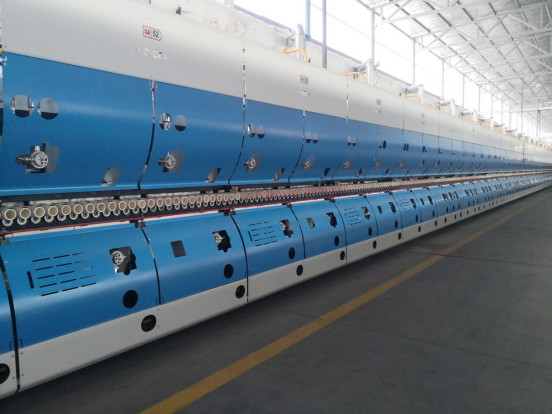
HLT&DLT prioritizes the application of advanced technology, seamlessly integrating intelligent, digital, and mechanical manufacturing technologies. This integration aims to continually enhance machinery production efficiency and reduce energy consumption, enabling ceramic enterprises to cut costs and increase efficiency.
With the operation of this production line, it is believed that it will further accelerate the enterprise's transformation towards the goal of "high-end industry, high-end products".
Looking ahead, Zhongpeng International Ceramics (Uzbekistan) and HLT&DLT are committed to deepening their cooperation. By fully leveraging their respective strengths, they aim to jointly explore new paradigms of technological innovation and industrial integration. Together, they will steadfastly promote the industry's development towards high-end, intelligent, and environmentally friendly solutions.
(HLT&DLT)