2023 Foshan (Tanzhou) International Ceramics Equipment and Materials Exhibition will be held grandly from May 30th to June 2nd at Tanzhou International Convention and Exhibition Center in China. Adhering to the product concept of "green, low-carbon, energy-saving and advanced digital & intelligent manufacturing", HLT&DLT Ceramics Machinery aims to exhibit and introduce advanced and popular professional machinery in the industry, and assist in the new model of intelligent and low-carbon production.
Consisting of "HLT Machinery, DLT Technology, HLT Technology and HLT Ceramics Technology", HLT&DLT Ceramics Machinery adopts a dual development pattern of "being specialized in single machinery and strong in whole production line". To help visitors grasp the pulse of the times, identify trends of industry and ignite the engine of development with technical innovation, what "special contribution" will it bring to the six zones of the exhibition this time? Be the first to know the new exhibits in green and low-carbon zone.
01 Ammonia-hydrogen Fusion Zero-carbon Combustion Technology
As a representative of high-end Chinese kiln brands, DLT has always focused on the energy conservation and emission reduction of kiln and dryer in the ceramic industry, made its own contribution to low carbon and reduction of energy consumption in the industry actively and assumed social responsibility initiatively. On December 27th, 2021, Foshan Xianhu Laboratory, Oceano Ceramics and DLT established the "Advanced Zero-Carbon Combustion Technology Joint Innovation and Research Center" together. Academician Yibing CHENG, a strategic scientist at Foshan Xianhu Laboratory, served as the center's director.Targeting the disruptive key technologies of zero-carbon combustion in ceramic kilns, the center will explore new directions for China's ceramic industry to achieve the carbon peak and neutrality targets.
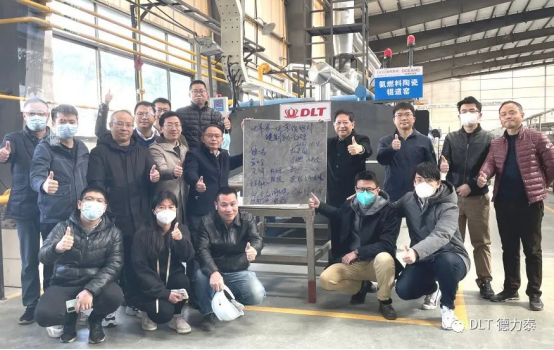
After nearly a year of technical research and innovation, the world's first "zero-carbon fired ceramic tiles" were produced in pilot scale at Oceano Experimental Center on December 23rd, 2022. The on-site testing by a third-party environmental impact assessment agency showed that the exhaust emissions of kiln were in full conformity with national standards. The second pilot test was completed successfully on April 18th and 19th, 2023.
The achievement has verified the practical feasibility of achieving the goals of carbon peak and carbon neutrality, and industrial application in the ceramic industry in the future, which is an important landmark for the industry. Firing ceramics with zero-carbon fuel is a disruptive innovation that fills up domestic and international blanks and opens up a new technical path for the ceramic industry and even the entire building materials industry to achieve the "Dual Carbon" goals. New technology is promoted as well in the field of building ceramics together with Monalisa Ceramics. Four parties will leverage their respective advantages through the "Joint Innovation and Research Center" and carry out mass production verification and application of the advanced low and zero carbon combustion technology in the field of building ceramics, so as to help the building ceramics industry to achieve the goals of "dual carbon".
02 Carboneutral Double-layer Roller Kiln
The Longest One in the World Currently
Benchmark in Respect of Both "Energy Efficiency and Digital Intelligence”
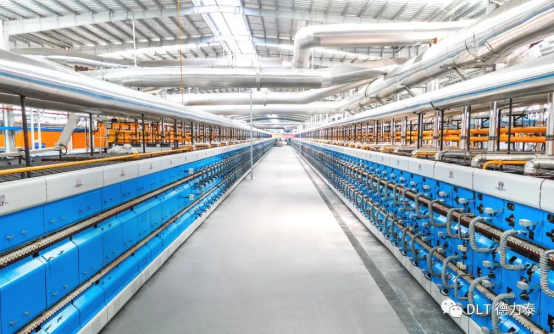
Benchmark in Respect of Both "Energy Efficiency and Digital Intelligence”
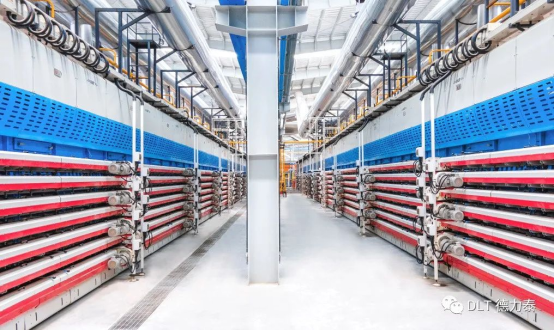
The Carboneutral firing kiln comes from hands-on experience of more than 20 double-layer roller kilns. Being combined with the advanced design concept of Italian ICF & Welco in double-layer kilns and the first-hand operation data of domestic kilns for sintered stone/ceramic board, as well as Carboneutral's design theory, Carboneutral firing kiln is developed to be a new generation of low-carbon and energy-saving double-layer roller kilns. It has opened up a new mileage of low energy consumption of double-layer kilns in the industry in multiple projects at home and abroad.
The new double-layer kiln comes with the advanced digital intelligent management system and a number of unique patented technologies to meet the high requirements that it will not fall behind others in the next ten years. It is the first in the industry to be equipped with DHR waste heat recovery system, PPC combustion air ducts group control system, OCE optimized combustion energy-saving system and other systems reasonably, and to use the best and reasonable refractories, breaking the restriction of traditional design thinking of kilns to achieve low-carbon energy saving, wide cycle range and strong adaptability. The new product can meet all kinds of customized flexible manufacturing.
Through the technical innovation, DLT has launched three sets of the world's longest (415 meters) double-layer kilns at Newpearl Group and Oceano Ceramics. Those double-layer kilns for sintered stone have solved a series of technical problems of ash contamination, thermal stability, cutting cracks and temperature interference between the upper and lower layers, and improved the synergetic benefits between equipment and green production capacity. The comprehensive energy saving exceeds 10%. The new product not only realizes carbon emission reduction and takes the social responsibility of actively responding to the national strategic goals of carbon peak and carbon neutrality, but also becomes a new benchmarking model that leads the transformation and upgrading of the building ceramics industry to green and intelligent manufacturing.
03 EM Series High-efficiency Self-circulation Seven-layer Dryer
The EM series multi-layer dryer is an outstanding drying device which combines the advantages of high efficiency, uniformity, high speed, energy conservation and strong adaptability to different products with numerous specifications and long drying cycle span. Especially the unique double outlets for heating air supply and self-circulation structure developed by DLT independently has features of good stability, fewer mechanical cracks and better regularity of unfired tiles. The normal production only needs to use the remaining heat resource in the kiln upon cooling and additional heat sources are unnecessary, which reduces the energy consumption and saves space significantly.
04 New 3HP Self-cleaning Gas-gas Heater
The new 3HP automatic cleaning gas-gas heater has overcome the technology bottlenecks, such as clogging from dirt, easy corrosion and low heat exchange efficiency, of ordinary gas-gas heaters. It can generate high-temperature clean hot air to heat the combustion-supporting air and dry the heat sources for an efficient reduction of energy consumption, and automatically clean the flue gas and dust of the heat exchanger on line in real time to maintain efficient operation.
(Huaying HUANG, HLT&DLT)